New staggering MMC study is just another reason why it has become essential to the UK construction industry
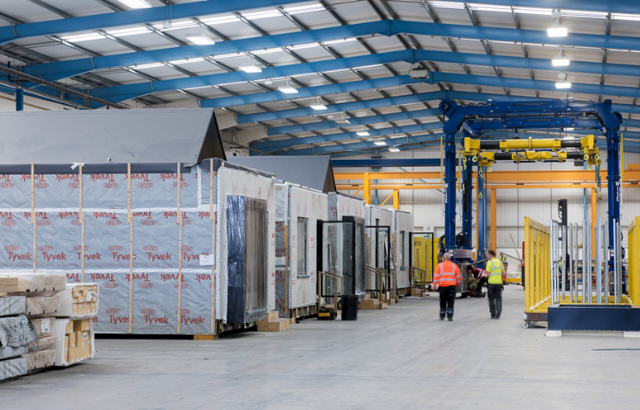
Anthony Lymer, a Business Development Manager at Protrade and specialist in the area of Modern Methods of Construction (MMC), has outlined the wealth of other benefits MMC can bring to the construction industry in the midst of a breakthrough study.
New research carried out by the University of Cambridge and Edinburgh Napier University showed that factory-produced homes can produce up to 45% less carbon than traditional methods of residential construction.
The study found that two modular housing schemes, consisting of a total of nearly 900 homes, saved a combined 28,000 tonnes of carbon.
Speaking about the statistics, Anthony Lymer said: “The result of these independent researches is a welcome and further much-needed addition to much of what has already been stated by many of the design and technology divisions within some of the country’s largest MMC manufacturers.
“This is yet another validation on why the Government is renewing its drive to tackle both housing shortages and the climate change issues – effectively, two key political agendas in one.”
As of 2022, the carbon emitted by the construction industry accounts for approximately 11% of global emissions, accounting for between 40 and 50 million tonnes each year in the UK alone.
This combined with the ongoing housing crisis and the fact that the Homes England programme, which is aiming to make a quarter of affordable homes from MMC, this breakthrough study represents another step in MMC becoming more influential in the UK’s construction scene.
This article examines what MMC actually is and analyses the key reasons why it’s entering a golden age.
First off, what is MMC?
Modern Methods of Construction is a wide term.
It covers a range of off-site manufacturing and on-site techniques that provide alternatives to traditional house building methods.
MMC (Modern Methods of Construction) and off-site manufacturing are nothing new. However, its adoption as the primary method of working across the industry has been accelerated by the need for construction to be far more efficient after a rough couple of years.
Off-site construction allows most construction phases to be undertaken simultaneously, all while site preparation, foundations, and utility connections are being prepared. Whole completed units can be built in a factory ready for final assembly and finishing in situ.
Also, construction doesn’t stop at residential properties – other important sectors include educational, social housing, custodial, health, and the hotel industry. All of which are benefitting from this method.
Remember the Huoshenshan hospital that was built in Wuhan in 10 days in 2020, as a result of the COVID-19 pandemic? That was down to MMC.
On a wide scale, with the huge demand for construction seemingly unachievable using traditional methods, MMC is widely recognised as a viable option to alleviate those demands.
Beyond environmental, what are the other benefits?
Although appearing almost daily in our news feeds, the climate change crisis, renewable energy, and sustainability have held a magnifying glass up to construction for many years now and the pressure for creating energy-efficient, low carbon emission sustainable buildings has never been so focused.
Focusing even on just the economics, though, there is enormous investment going into it in the UK. And for good reason too.
There are three obvious benefits to the country and the economy:
- the first is the commercial gain
- its ability to give companies a competitive edge
- improve the sector’s capability to meet demand after a pandemic that saw multiple projects mothballed and kicked into the long grass during 2020 and 2021.
Off-site manufacturing techniques have progressed significantly over the last few years, moving it on significantly from a time when it held a tarred reputation and was used mainly as temporary accommodation; your portacabins and the like.
However, innovative technology in MMC is making regular advancements in the fight to reduce our ecological footprint. Reducing vehicle movement also minimises disruption to local residents, road congestion, and carbon emissions.
One of the bigger benefits is the controlled factory process, which drives a highly consistent quality finished product with minimal defects.
Buildings are scrutinised to the highest standards prior to delivery and it’s not unusual to drive past a plot one week and find a completed property with a family car in the driveway the next!
The ongoing supply chain issues have driven up interest in Modern Methods of Construction
It’s no secret that the supply shortages and lead times construction has faced over the last two years caused issues with projects across the country, with housing associations and local authorities grappling with limited supplies as well as soaring prices that reached a 40-year high for the industry.
There was an impact on a much smaller scale, too. Last October, the price of silicone went up 39% in price, fixings made out of steel increased by 25%, and channel and bracketry used in steel building systems have shot up over 60% since January 2021. If you also look at raw materials, like polymers and monomers that go into making PVA and acrylics, they’ve also had price hikes by more than 40%, too.
The prices we’re seeing in the market are not going to change. The shortage that is being faced isn’t going to disappear.
This, alone, is creating a new wave of competition and demand for labour and raw materials – one that will even outweigh the problems that were faced last year.
But, the reality is Britain needs to build and construction will continue to be a vital sector for the UK economy. It’ll simply cost more. In order to combat these ongoing problems, the onus is on construction professionals to shift to a more viable option.
That obvious alternative is off-site manufacturing.
MMC is no longer deemed a fad… it has now become essential to our industry’s future
Bringing change to the traditional processes of construction is clearly a slow burner but disruptors to the market have already proved that high-quality, insurance-accredited products can be manufactured to increase the adoption of offsite and pre-manufactured solutions.
It’s not what some would deem a ‘fad’. Millions of pounds worth of investment validate that but the message needs to be repeated.
Back in 2018, the Government laid out its plans to combat the growing housing crisis in the UK. However, since the pandemic hit, off-site manufacturing’s role has been accelerated to a point where it, in my opinion, needs to be considered essential.
A report by Savills, one of the biggest retail estate agents in the UK, showed that the proportion of new homes built using MMC was currently between 6-10%. In the new builds market, that is going to increase significantly, especially with the Homes England programme, which is aiming to make a quarter of affordable homes from MMC.
We know Lloyds Bank has the ambition to become the biggest landlord in the country and as part of their intention to buy 50,000 homes over the next decade, the likelihood is they’re going to need to build some of those properties.
As well as dealing with those ongoing supply shortages and price hikes, using traditional building methods to fulfil their needs is not commercially viable. Missing out on rental income is a huge incentive for businesses and institutions to get the homes built rapidly, and there’s no faster construction method than off-site manufacturing, which strips away the myriad of factors, like weather, site access, permissible working hours, and noise pollution, that can impact a project.
Concerns over build quality are no longer relevant, with many off-site homes now offering a mortgageable 60-year warranty. Even hospitals, schools and commercial properties are looking toward modern methods of construction.
Why? Because the possibilities are endless.
Written by Anthony Lymer, Business Development Manager at Protrade.
All images have been downloaded and approved for editorial use by Shutterstock and Unsplash.