Impact Driver vs Drill: which one do I need? [2025]
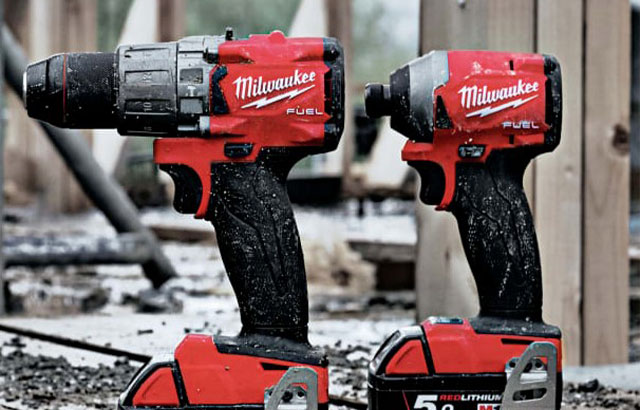
Whether you’re a have-a-go handyman or an experienced tradesperson, you’ll almost certainly have heard of, if not used, an impact driver and a drill. The most popular cordless set sold in the UK today is the combi drill and impact driver ‘twin kit’. This duo of ‘drill and driver’ often constitutes the foundation of most cordless tool kits, as a huge range of power tool accessories can be used with these two machines alone.
‘It doesn’t matter whether you work predominantly on site or in the workshop. There will definitely be a time when having both machines available will make completing a particular task, faster, safer or easier.’’ Des Duddy, Joint Managing Director
Over the last year, we have sold 32% more combi drills than impact drivers, which indicates the versatility of the combi drill.
But what is the difference between an impact driver and a drill? In this piece, we break down everything you need to know about impact drivers vs drills, and explore the different uses, along with their advantages and disadvantages, including:
Impact Driver vs Drill – Size
When I first tried to explain each tool’s characteristics, it prompted a sigh and plenty of head-scratching. Despite the machines looking similar, they are in fact quite different.
The most obvious difference between the two power tools is the physical size – I’m primarily referring to the length of the machine from the tool retaining end to the back of the casing.
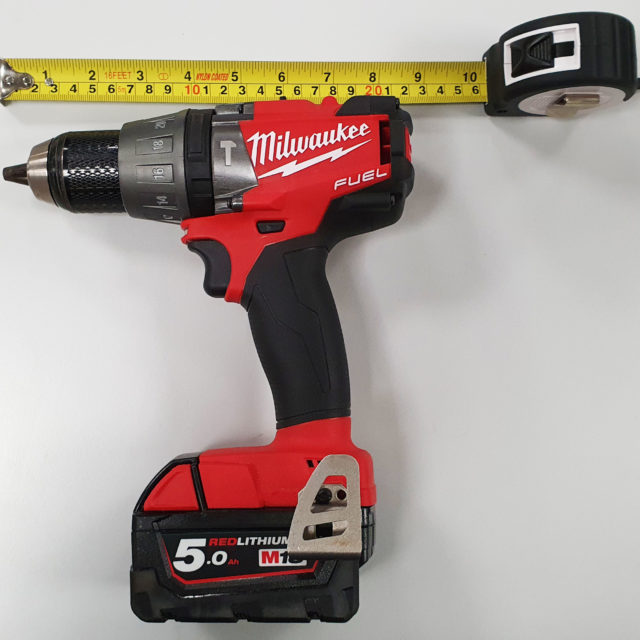
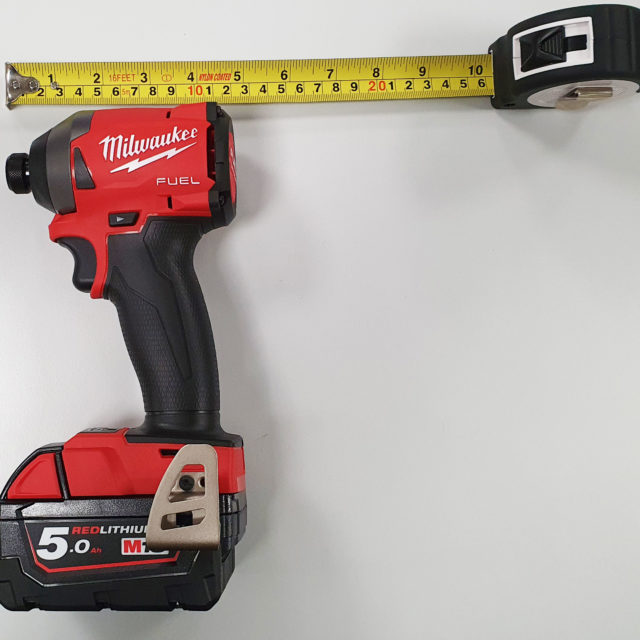
What is an impact driver?
Due to the internal workings, impact drivers can be made with a very short body, which allows access into tight spaces and reduces the weight of the machine substantially. This compactness and lightweight can make an impact driver invaluable when working between joists, inside cabinets or operating in overhead applications.
What is a drill?
A drill is primarily used for drilling and boring applications and typically is better than an impact driver for these tasks. In its most basic form, a drill is a motor connected to a chuck via a gearbox. A variable speed trigger is a common feature of most drills. For the purpose of this blog, the drills we refer to could be a combination drill or drill driver – in other words, a drill with or without a percussion hammer facility.
Impact Driver vs Drill – Front end
Another visible difference is at the front of the tools.
Impact driver
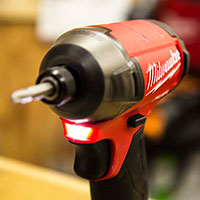
The impact driver has a ¼” hexagon bit retainer.
Drill
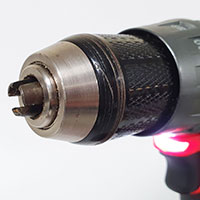
The drill uses a three-jaw chuck to hold the power tool accessory. A three-jaw chuck is used to hold round, hexagonal, and even triangular-shaped shanks. The self-centring nature of the 3 jaws is to hold bits tightly, and dead-centre of the chuck for precision drilling.
The opening and closing action of the chuck makes it possible to grip varying diameters of cylindrical shanks found on drill bits, triangular shanks on many arbours and hexagonal shanks for paddle stirrers, bit holders and screwdriver bits.
The entire range of accessories available for use with a drill chuck is far too numerous to list here – but if the accessory has a shank with any of the aforementioned shapes, the chuck can undoubtedly grip them.
Impact Driver vs Drill – Working mechanisms
The working mechanisms of each machine are where the two tools are very different. Unsure of how best to describe this, I headed to our service centre and sought the expertise of Simon Wilde, who heads up our team of factory-trained fitters.
With over 35 years of experience, Simon has seen the insides of literally thousands of power tools, and I hoped he would provide me with a simple explanation. The first thing he did was to open the cases of both tools, so I could see the different parts of each machine.
Both machines have a battery-powered motor driving two completely different torque delivery systems.
Impact driver
Impact drivers deliver bursts of torque by releasing energy from a spring. This powerful action causes rotating hammers to strike an anvil many times a second. This is perfect for applications which require high torque without resistance being passed back to the operator.
This video clip, from the premium professional brand Festool, illustrates the mechanism very well.
Drill
The drill maintains constant turning torque using gears. To put into layman’s terms; imagine placing your hand on a brick wall, then push and keep pushing – that’s how the drill delivers its power. Now imagine punching the brick wall (I said imagine) – this is how the impact driver works. One is a continual ‘push’, and the other is a short sharp ‘punch’. Check out this video of a Festool PDC drill to see how the mechanism works.
Impact Driver vs Drill – Torque delivery
The method by which torque is delivered is what separates the two tools, and ultimately highlights their advantages and disadvantages.
Impact driver
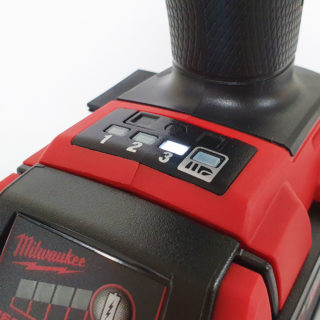
Impact drivers deliver the highest torque when operated at their fastest speed, as this allows the biggest impact of the hammer against the anvil. Drills, on the other hand, have the highest turning force when in the lowest and slowest gear.
Although impact drivers can also be used for drilling applications, when used in conjunction with ¼” hexagon shank drill bits, the stop-start rotations are more likely to leave an undesirable surface finish. Optimised drilling speeds are often compromised with impact drivers too.
Most users of impact drivers love the fact that even when driving in large screws, they don’t have to wrestle with the machine. I was recently speaking to a customer who commented…
“I only use an impact driver when I work on steps or ladders, as there is very little risk of the machine kicking back violently. I’ve seen other workers fall when bits have snagged.”
Because impact drivers deliver their torque in bursts, lasting a fraction of a second, there is no equivalent force being transmitted back to the user – making them much safer to hold with just one hand.
The main advantages of the impact drivers torque delivery system means:
- Screwdriver bits are less likely to jump out of fastener heads.
- Very little weight is required behind the tool.
- It can be used at arm’s length – ideal when you need to tighten or loosen something in a difficult-to-reach area.
This lack of feedback is great in most applications, except precision screwdriving.
More recently, impact drivers are being equipped with different speed settings to give the user more control in screwdriving applications. Milwaukee impact drivers also have a very clever feature, which is a special setting for self-drilling screws. The ‘auto-setting’ is designed to prevent over-tightening and avoid crushing washers on the underside of roofing tek screws.
Drill
Drills are ideal for drilling and boring applications, as the constant turning force will achieve a smoother, more accurate and cleaner hole. Precise screwdriving applications are also best suited to a conventional drill, as rotational speeds are more easily controlled, torque is maintained at slower speeds, and you receive feedback from the machine – more on that later.
Unlike an impact driver, if a drill is turning a fastener using 30Nm of torque, an equal force is being transferred back to the operator. The feel of a drill makes it more obvious when you’re about to crack a delicate material or overtighten and snap the head on a small screw – something you do not sense when using an impact driver.
Impact Driver vs Drill – Torque
It’s not uncommon or unreasonable for users of power tools to make purchasing decisions based on the comparison of a tool’s specification sheet – the fastest RPM and the highest torque number must make it the best… right? Well, not quite.
Impact driver
Impact drivers are often praised for their high torque, and indeed they can deliver powerful ‘bursts’ of turning power, especially when you consider how compact they are. However, torque figures on specification sheets can be confusing depending on how the torque is measured. A great example of this is hard and soft torque.
Soft torque
Maybe the best way to describe this is to imagine driving a woodscrew into timber. As the screw is driven deeper, more and more torque is required, gradually increasing until the head reaches the material – this is referred to as soft torque.
Hard torque
Now consider driving a threaded bolt into a pre-tapped steel plate; once the thread is engaged there is very little resistance encountered as the bolt passes freely through the threads.
However, when the underside of the bolt head eventually meets the steel plate it does so with a ‘whack’, as there is no absorption of force by the base material. The torque at that instant increases dramatically, giving a very high reading – this is considered hard torque.
The graph below isn’t meant to be an accurate representation, but it illustrates the point.
Most torque figures for impact drivers quote a hard torque ‘peak power’ figure, which only lasts for a fraction of a second. Therefore, this ‘high’ figure cannot be directly compared with some of the most powerful drills which, on paper, might ‘only’ be able to offer a meagre 60Nm of torque.
Drill
The difference is: drills can maintain the torque level throughout the entire turning process. Many people are often surprised to see a powerful drilling machine continue to drive in a large construction screw, when an impact driver with a much higher torque specification, has long given up. It’s the continual turning power that makes this possible.
Impact Driver vs Drill – Noise
If you’ve ever heard an impact driver or drill in action, you’ll instantly recognise the noisy hammering action of the impact driver compared to the drill.
Impact driver
If you were to ask a user of an impact driver, or indeed anyone working in an area where they are being used, I’m certain they would mention how noisy they are. I’ve even heard some users refer to impact drivers as ‘rattlers’ because of the sound they make. The principle of a metal anvil being struck repeatedly by spinning hammers is bound to generate noise – and this is one of the drawbacks of an impact driver.
Drill
The noise from the drill comes from the motor and gearbox combined, and although you can hear it, the sound levels are certainly more bearable. Whilst we would always recommend wearing ear protection in any drilling or driving application, drills are certainly quieter than impact drivers. The exception is when impact or percussion drilling in masonry, with a combi drill.
What about Pulse Tools?
More recently, a handful of power tool manufacturers have launched tools that look just like an impact driver, but much quieter in use. Pulse tools have been around for some time but were only traditionally found in pneumatic machines – often used on assembly lines.
Unlike impact drivers, utilising the ‘strike’ of a hammer on an anvil, pulse machine force hydraulic oil through veins to create a ‘wave’ of incompressible liquid. The wave then pushes two paddles around a sealed chamber, a quarter turn each time.
We’ve already talked about the continual push of a drill and the punch of an impact driver; pulse tools are somewhere in-between, giving more control to the operator in screwdriving applications. The other benefits of Pulse technology are:
- Noise is cut in half
- Mechanical wear is reduced
- Less vibration is passed onto the user
The downside is: torque is reduced making these machines ideal for small to medium-sized woodscrews and small self-drilling screws or self-tappers.
For these specific applications, tools like the Milwaukee Fuel Surge might just be the perfect screwdriving companion.
Impact driver vs Drill – Which one do I need?
Having highlighted the key features and differences between impact drivers vs drills, one could argue that the choice of tool will ultimately be decided by the amount of time the operator spends drilling or driving.
Combi drill
- Larger and heavier
- More versatile as chuck accepts all types of accessories
- Better for drilling, boring and precision work
- Must use two-handed in high torque applications
Impact driver
- Very compact and lightweight
- Effortless screwdriving
- Single-handed use with no kickback
- Only accepts ¼ hex shank accessories
- Noisy
However, one application often precedes the other, which could explain why the drill and impact driver partnership is ubiquitous on the job site.
If you’re a professional tradesperson, who is serious about efficiency and having the right tool for the job, you really should have both.
Related Products
Protrade stocks an extensive range of professional impact drivers and drills, click on the categories below to explore our variety.
While we have an informative and easy-to-navigate website, we also understand that our customers appreciate being able to visit a bricks-and-mortar environment, have a chance to ask questions and receive face-to-face advice, or simply collect goods for immediate requirements.
We have depots across the East Midlands in Burton, Chesterfield, Derby, Mansfield and Nottingham, so, why not come along and meet our team who will help you find everything you are looking for?
Related Articles
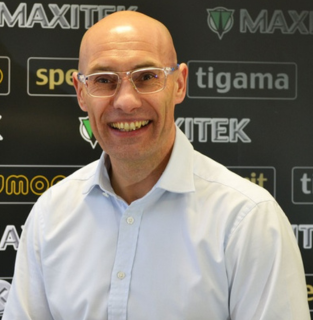
Joint Managing Director, Protrade
Des has over 30 years of experience at Protrade, having worked in the capacity of Sales Co-ordinator, Account Manager, and product development, culminating in being appointed Joint Managing Director in 2018.