From delamination to litigation
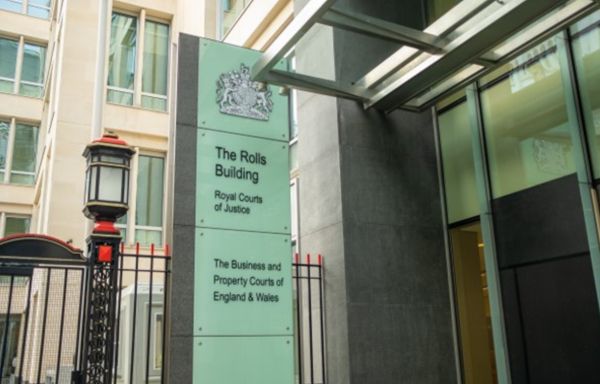
Reading Time: 8 Mins⏱️
The 10-year saga of faulty spray glue
There are many consumable products used throughout the construction industry, many of them low-cost and underappreciated. The reality is, when they go wrong or fail, they can cause unimaginable problems with enormous costs attached.
As a supplier of professional products from recognised brands as well as our own, the last thing we expect is for any of them to cause hardship.
But in 2011, one such product did. In this article From delamination to litigation: the 10-year saga of faulty spray glue’ joint managing director Des Duddy addresses how it has taken more than 10 years to find a resolution, not just for Protrade, but more importantly for Protrade’s loyal and trusted customers.
Behind the 10-year saga of contact adhesive failure
This isn’t a story you read about often.
This is a story about a product that went horribly, horribly, wrong.
Most of us have heard the phrase ‘does what it says on the tin’.
But what happens when a product you buy doesn’t?
On a small scale, it can cause a great deal of annoyance and loss of trust. But on a larger scale, it can have significant ramifications that transcend annoyance. It can cause a heap of problems for your own business and reputation.
A history of contact adhesives and contact adhesive spray canisters: an introduction to the UK market
Before we begin, we need to start with some context.
In the woodworking and shopfitting industry, pourable contact adhesives have been used for attaching decorative laminates to furniture for decades.
These treacle-like adhesives are applied to both surfaces and once the solvent carrier has evaporated, the substrates are pressed together – hence forming a bond ‘on contact’ with one another.
Although effective, the glue has a pungent smell, the application time is long, and you need some skill to make sure an even layer of glue is applied.
Around the year 2000, spray adhesive canisters came to the UK.
By attaching a spray gun and hose to one of these self-pressurised containers, like a large aerosol, operators could complete laminating tasks ten times faster.
For obvious reasons, they proved incredibly popular and have become an essential product in the joinery and shopfitting industry. For over ten years these revolutionary products proved their ease of use and remained trouble-free.
Until they didn’t.
Widespread spray glue failures
In late 2011, our customers began to inform us that they were experiencing serious bond failures after using a canister adhesive we had supplied.
The delamination occurred months after the glue had been applied and affected many different materials. This was a generic formulation purchased by many distributors right across Europe.
The failures we were being made aware of were not confined to us. In fact, they were widespread, causing repair works estimated to be in excess of £30 million.
The canister filler was made by a company called AFT and the adhesive was alleged to have been manufactured by Bostik, although there was speculation that other adhesive manufacturers were also involved.
The possibility of AFT filling canisters with more than one manufacturer’s adhesive made it virtually impossible to trace the key ingredient and assert where the issue was being borne from and who was ultimately liable for damages.
Unfortunately, this complicated situation meant that only a handful of contractors ever received compensation which amounted to a few thousand pounds – grossly disproportionate to the £30 million losses they had incurred.
The launch of a new spray adhesive, PRO33NFA
As our organisation had been involved in these catastrophic glue failures directly, we were very aware of the huge costs and reputation damage that our customers and ourselves were exposed to.
Having changed our supplier immediately, we embarked upon formulating a new product – a revolutionary spray glue canister that had to contain adhesive limited to a single manufacturer, have a higher percentage of resin to promote stronger bonds and finally, it needed to spray well.
Most importantly, our new product would reassure customers that spray glues were reliable, easy to apply, and contain raw materials that were fully traceable. Sanglier would be the formulator and canister filler, with them engaging Apollo Chemicals as the adhesive manufacturer, thus creating a fully pressurised spray glue system.
Our new product was to be called PRO33NFA:
Professional with 33% solid content, and because the product had been well considered it would give our customers No F***ing Aggro.
Oh, how wrong we were!
The product was launched in February 2013 and was initially well-received by our customers. However, sadly, in late December of that same year, our delight turned to dismay.
One of our customers complained that various pieces of laminate that had been applied using the PRO33NFA had simply come away from a number of display counters, leaving behind a dry, powdery substance.
We investigated this particular case immediately but were subject to more complaints from other customers in the first quarter of 2014. It was suggested by the manufacturer, that our customers were simply misapplying the adhesive which, as experienced applicators, we were sceptical about.
Further to numerous site visits where we obtained material samples that showed worrying similarities to the AFT/Bostik failures, we withdrew the product from sale in early March 2014.
Reviewing the chemical analysis
Having been scarred already by the Bostick/AFT glue failures, we actively sought to get as many canisters as possible back from customers along with material samples, which were carefully logged and retained for forensic chemical testing.
Highly sophisticated and very expensive chemical analysis including Fourier Transform Infrared Spectroscopy (FTIR) and Nuclear Magnetic Resonance (NMR) analysis, was used as a means to confirm that the degraded adhesive on the sample boards was ours and, hopefully, offer us some insight as to why the product was degrading prematurely.
Ultimately, these tests proved that the adhesive was PRO33NFA and that the isoprene levels had significantly diminished due to oxidative degradation.
Having serious concerns about the rising number of calls we were receiving from our customers, we engaged with our insurers Allianz who, considering the potential for damages arising from multiple adhesive claims, instructed their legal representatives DAC Beachcroft LLP to represent us.
After months of hard work and detailed assessment, the loss adjusters awarded total damages of £2.1 million to contractors that had experienced delamination through the use of PRO33NFA adhesive.
Claims of delamination through glue misapplication
Throughout the entirety of this case, our claim of being sold a defective adhesive that was not fit for purpose was rebuffed by the manufacturers, with the insistence that our customers had misapplied the product, despite them having applied similar products without issue for many years.
Indeed, The Honourable Judge Pelling KC referred to such in his judgement:
‘The point is that delamination occurred because of a defect in the product. That is the only explanation that on the balance of probability explains the widespread failures that occurred when this product was used, which did not occur when other spray-applied adhesives were used by the same operatives in the same applications using the same techniques.”
To further discount the cause of delamination through misapplication, we, ourselves, applied adhesive from various batches that had been collected from customers onto test boards, ensuring application instructions were followed precisely.
Sometime later, these boards were retrieved from storage and examined by a consultant scientist. In each case, the adhesive had failed, and the laminate had separated from the substrate – these test pieces were subsequently used as evidence.
Although we had exclusive rights to the formulation in the UK, the adhesive was sold to a distributor in the Netherlands under a different name. During the process of disclosure, we learned that this distributor had also experienced many glue failures with a number of its customers.
A decade-long journey to reach closure
Unfortunately, despite overwhelming evidence to suggest the adhesive was faulty, no resolution could be found, leading to a hearing at the High Court of Technology and Construction in October 2022 which lasted four weeks.
The contractual chain would mean that we would be a claimant against Sanglier, who in turn would be claiming against Apollo. Sanglier remained steadfast in their misapplication theory to refute our claim, yet they used the notion of having been supplied a defective adhesive by Apollo when pursuing their own.
As there were so many affected customers, the hearing would focus on just six claimants, the result of which would determine how to proceed with all the rest.
The court also considered expert evidence presented, which involved highly complex chemistry issues in respect of the nature of the defect in the adhesive, upon which there was significant disagreement. The judge took a step back from this evidence, and accepted that it would be:
‘ staggeringly unlikely…”… that “…suddenly when taking up [the adhesive], and only when using [the adhesive], many if not all of the joiners and fabricators employed by the [end users] forgot en masse how to use sprayable PSAs in a proper and workmanlike manner..”
It took until March 2023 for judgement to be handed down and we were successful on all points. Incredulously, from the first notification of failure through to reaching a conclusion, nearly a decade had passed – thank goodness our affected customers didn’t have to wait as long!
Sanglier was instructed to pay the sum of £2.69 million to our insurers, and the remaining customer claims amounting to another £1.2 million were to be agreed upon within a specified timeframe.
Final thoughts
The fact we had suitable insurance cover in place and received expert legal advice cannot be overstated.
This allowed our customers to be compensated for the immense stress and financial pressure these glue failures placed upon them and their businesses. I understand that no settlement truly recompenses an organisation that has been placed in such a difficult situation, but I do take some comfort that our customers did at least receive something.
Although the size of our organisation pales into insignificance when compared to world-renowned adhesive manufacturers that were part of the 2011 failures, we chose to face the music and not abandon our customers – something I am very proud of.
I believe the loyalty and support of our amazing customers, the commitment from colleagues, and our dogged determination, enabled Protrade to navigate through this challenging situation, one of the most trying in our 50-year history. To everyone involved, I can’t thank you enough.
A full review of this case can be found here.
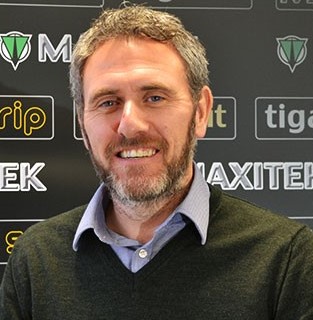
Joint Managing Director, Protrade
Craig has over 30 years of experience at Protrade, working in various departments including sales, procurement, and marketing, and ultimately becoming Managing Director in 2008. Following the merger of Protrade and Joinery Fit-Out Supplies in 2018, Craig is now the joint MD of the company.