Chop Saw vs Mitre Saw: which one do I need?
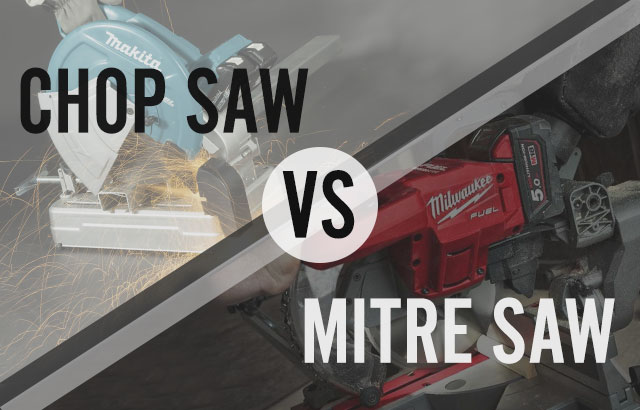
In this piece, Des Duddy breaks down everything you need to know about chop saws versus mitre saws, exploring the different applications and types, along with their advantages and disadvantages. Specific tools covered include:
- Abrasive chop saws
- Tungsten carbide tipped (TCT) chop saws
- Compound mitre saws
- Sliding compound mitre saws
There are many colloquial terms used in the construction industry. Having joined this industrial sector 28 years ago, I remember trying to get to grips with lots of different names for the same product. In fact, I’m still picking them up now. Two power tools which suffer from such a general description are chop saws and mitre saws.
I am only going to discuss abrasive and TCT chop saws in this article, saving slower revolutions per minute (RPM), high-speed steel (HSS) cold saws for another time. The definitions and applications apply to both corded and cordless machines.
Chop Saw vs Mitre Saw – The Material it’s Designed to Cut
A remarkably simple and defining feature between a chop saw and mitre saw, is the material they are designed to cut.
In the case of the chop saw, that material is metal – predominantly steel.
Mitre saws are typically used for wood, although they can also be used on plastics and non-ferrous metals.
What is an Abrasive Chop Saw?
As the name would suggest, an abrasive chop saw, commonly referred to on-site as a bacon slicer, uses a large and abrasive cutting disc to cut through the material. The abrasive disc, which is made up of grit, resins and reinforcing fibres, grinds its way through the metal. Although it is a well-established and effective design, this cutting method does have some downsides.
Arguably, the most noticeable ‘con’ of an abrasive chop saw is cutting speed. Abrasive cutting discs will eventually make their way through almost any material, but compared to a specialist TCT blade, they are much slower. The grinding process can also create razor-sharp burrs which are a cut hazard. Any grinding process creates heat and in the case of a chop saw, it leaves the base material remaining hot to the touch after the cut has been made. This heat generation can also discolour or damage surface finishes making them unsuitable for painted metal sections.
By nature of the disc’s construction, the diameter of the blade gets smaller as more cuts are made. This will eventually cause a substantial reduction in the cut capacity of the machine.
Due to the machine sparking, a hot works permit may be required on some sites. Despite the blade drop-down being fixed at 90°, angle cuts of up to 45° can be made by adjusting the clamp on the base of the machine.
Advantages of Abrasive Chop Saws
- Low purchase price
- Will cut very thick material and thin-walled sections without snagging
- Abrasive discs cut a multitude of materials
Disadvantages of Abrasive Chop Saws
- Slow cutting speed
- Cutting capacity reduces as the disc wears
- Creates sparks, dust and burrs
What is a TCT Chop Saw?
Many years ago, the sight of a TCT blade heading towards a piece of steel would have sent a shudder down the spines of contract managers and workshop supervisors.
The only circular saw blades baring teeth and designed for cutting steel, were made from HSS and used on low RPM, flood cooled cold saws. That changed some time ago when several manufacturers were able to develop machines that worked at higher RPMs and featured TCT blades. No lubrication was needed, due to the high-temperature resistant carbide teeth – hence the term ‘dry cut’.
One of the key target markets for this tool was the cutting of strut channel and threaded rod – an application regularly untaken by electrical and mechanical contractors. Compared to the traditional bacon slicer and good old-fashioned hacksaw; this new machine cut quickly, left no burrs, and created very few sparks without any dust. Since then, the TCT dry cut chop saw is now commonplace in metal fabrication workshops, racking companies and shopfitters. Most machines come equipped with a blade designed for cutting mild steel. Specific stainless steel cutting blades are available, although due to the nature of this material, blade life is compromised.
A well-maintained blade is virtually spark-free during the cutting process, but some sparks can still occur – therefore a hot work permit may be required. Like the abrasive chop saw, these machines are mostly used for 90° cuts, which is why the blade drop down is fixed at this angle. Using the same clamping system as the abrasive chop saw, angle cuts of up to 45° can be made.
Advantages of TCT Chop Saws
- Fast cutting
- Constant depth of cut maintained
- Blades can be re-sharpened
- Burr-free, dust-free and very few sparks
Disadvantages of TCT Chop Saws
- Limited blade life on hard materials
- Liable to snag or tear on very thin materials
Accessories to go with a Chop Saw
A dedicated, mobile cutting station helps to reduce noise and confines dust, sparks and cutting chips – providing a safe working environment.
What is a Mitre Saw?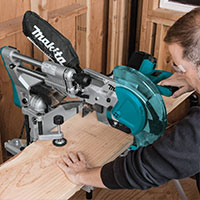
Whereas chop saws are rugged and relatively simple tools, mitre saws are designed and manufactured to make precision cuts at many different angles.
Although a mitre saw can cut non-ferrous metal when used with the correct blade, they are most often used by joiners, kitchen fitters and cabinet makers to cut wood.
“92% of our mitre saw blade sales are for wood and wood-based materials.” Des Duddy – Protrade Joint Managing Director
What is a Compound Mitre Saw?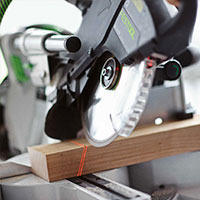
A compound mitre is the combination of a mitre and bevel cut. The mitre is made by rotating the base of the machine between 8 o’clock and 4 o’clock. Although the magic number for mitres seems to be 45°, many mitre saws are capable of cutting angles up to 60°. Bevel cuts are made by tilting the blade from 90° vertical through to a minimum of 45°, and often up to 48° – incorporating all the angles in-between.
Being able to make a compound mitre cut is ideal for applications such as cutting crown mouldings, or working on projects such as loft conversions, where angles of the walls and pitches of the ceiling must be considered. This is where the extraordinary angles of 31.6° and 33.9° featured on the gauges of some mitre saws come into play.
What is a Sliding Compound Mitre Saw?
A sliding compound mitre saw can perform the same mitre, bevel and compound cuts as a non-sliding compound mitre saw, with one additional feature. The sliding function increases cutting width capacity by allowing the motor unit and attached blade to travel along telescopic rods.
As many slide compound mitre saws rely on being portable, the sliding mechanism is an ingenious way of offering very wide cuts, whilst keeping the machine relatively compact.
Mitre saws are classed as single or double bevel saws. Single bevel machines can tilt to the left only, whereas double bevel units can tilt left and right. The double bevel feature can be useful as it negates the operator having to flip the workpiece over when left and right bevel cuts are required.
Protrade stock an extensive range of corded and cordless mitre saws. Below are the most popular, and arguably the best, 10” sliding mitre saws available from Makita and Milwaukee – using mains and battery power:
Makita DLS110 & LS1019L 260mm Slide Compound Mitre Saws
Milwaukee M18FMS254 18V Fuel 254mm Slide Mitre Saw
What size Mitre Saw do I need?
It really depends on the size of workpiece you’re cutting.
Blade diameter is the most critical measurement in relation to cutting depth. The larger the blade, the deeper the cut – this is simply because there is a greater distance from the edge of the blade to the clamping nut in the centre. When the workpiece hits the clamping nut, it prohibits the blade from going any deeper. You can get an idea of how deep a saw will cut, simply by looking at the blade diameter. For example, a 12” sawblade is capable of making a 4” cut, depending on the material dimensions and shape.
Blade sizes for mitre saws typically range from 190mm to a whopping 305mm. Ultimately, the best size for you will depend on the type of work you regularly do.
A kitchen fitter will probably never need the cutting capacity of a 305mm sliding compound mitre saw, and probably wouldn’t want to carry this heavier and bulkier machine in and out of people’s houses. Therefore, a compact 260mm compound mitre saw or even a 190mm slide compound mitre saw could be all the machine they ever need.
Conversely, a site joiner or carpenter – that may need to cut tall skirtings and joists – are more likely to choose a sliding compound mitre saw with at least a 10” blade.
Trade | Machine | Accessory |
Kitchen Fitter |
|
|
Shop Fitter |
|
|
Site Joinery |
|
|
Accessories to go with a Mitre Saw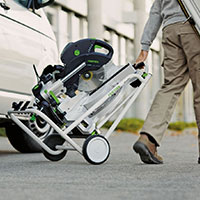
Mitre saws are known for creating significant amounts of dust; connecting your saw to a suitable dust extractor will help to keep the workplace clean and reduce the chance of dust inhalation. There are also various types of mitre saw stands available – many offering workpiece supports as well as various integrated transportation options for on site use.
Chop Saw vs Mitre Saw – The Verdict
Now we have compared the differences between a chop saw and a mitre saw, deciding which type of machine you need should be easy.
What will require more consideration is which machine you select. In terms of the chop saw; this will largely be dependent on your budget and the material you regularly cut. On the other hand, a mitre saw purchase will be led purely by the application and workpiece dimensions.
For any further help or advice on which type of saw is best for you, please don’t hesitate to get in touch with us. With nearly 50 years of experience, we’re confident in pointing you in the right direction.
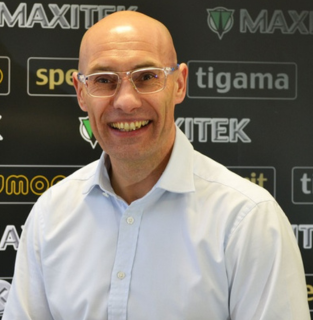
Joint Managing Director, Protrade
Des has over 30 years of experience at Protrade, having worked in the capacity of Sales Co-ordinator, Account Manager, and product development, culminating in being appointed Joint Managing Director in 2018.